-
✔ Complex Geometries
-
✔ Highest Precision
-
✔ Versatile Material Processing
-
✔ Oil Bath Erosion
-
✔ Fine Wire Processing
-
✔ Fast and Reliable Production
What Makes Retero Unique?
At Retero GmbH, we offer unmatched accuracy in micro-erosion, supported by cutting-edge technologies and years of experience. Our ability to process parts with wire diameters ranging from 0.02 mm to 0.10 mm places us at the forefront of the industry.
Swiss Quality
The ISO 9001 and 13485 certificates confirm what is absolutely self-evident to us every day. We adhere strictly to the quality management regulations for providing products that must meet regulatory requirements, as well as for the manufacturing of medical devices. We consistently comply with the rigorous production processes and the requirements of detailed documentation.
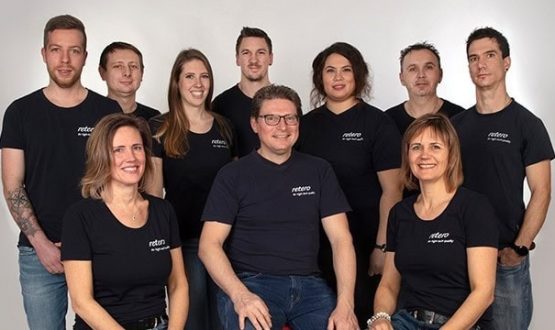
About Retero GmbH
Who We Are
Retero GmbH is your trusted partner for precision and innovation in micro-erosion. With decades of experience and state-of-the-art technology, we offer customized solutions for the most demanding projects.
-
Highest Precision: Micro-erosion for the smallest components with tolerances up to +/- 0.001 mm.
-
Complex Geometries: Creation of intricate contours, tiny radii, and minimal bores.
-
Versatile Material Processing: Working with materials like titanium, hardened steel, and conductive ceramics.
-
Efficient Production: Fast and reliable manufacturing of prototypes and small series.
-
Experience and Expertise: Decades of expertise in micro-erosion.
-
Quality and Reliability: ISO 9001 and ISO 13485 certified for the highest quality standards.
-
Customer Satisfaction: Customized solutions and top-notch customer service.
Applications
Our micro-erosion technology is used in many industries that require the highest precision. In the medical technology sector, precise components for life-saving devices are manufactured. The watchmaking industry uses our technology for tiny gears and mechanisms. In mechanical engineering, tool and mold making, as well as engine manufacturing, companies benefit from our fine micro-drilling capabilities. Materials like titanium and ceramics are processed with the utmost care to produce products of the highest quality.
Micro-Erosion with Retero
In micro-erosion, we work with minimal dimensions and maximum precision. The smaller the components, the greater the demands on precision, repeatability, and efficiency.
Thanks to extensive know-how and innovative techniques, we can realize standardized solutions as well as custom projects according to client specifications. In the field of micro-erosion, we are capable of processing parts with the smallest wire diameters ranging from 0.02 to 0.10 mm, as well as micro-drillings using the smallest carbide electrodes from 0.10 mm and larger.
Material removal through erosion offers many advantages. First, it can be determined and controlled with absolute precision. Unlike milling or honing, even complex geometric shapes, extremely delicate contours, tiny radii, or minimal bores can be executed.
At Retero, this manufacturing technique is already being used in many industries:
- Mechanical Engineering
- Tool and Mold Making
- Engine Manufacturing
- Medical Technology
- Watchmaking Industry
This process is also used in automotive manufacturing and component production for the aerospace industry.
The range of processable materials is almost unlimited; the only requirement is their electrical conductivity. Even the hardest materials, such as titanium, hardened steel, or other hard metals, as well as special metal alloys and conductive ceramics, can be eroded. Processing such materials with other machining techniques would require much more effort or would simply be impossible. A distinction is made between wire erosion, die sinking, drilling erosion, and disk erosion.
Micro-erosion fine wire erosion tweezers ophthalmology inox
With this work technique, dimensional deviations are only within the range of just a few thousandths of a millimeter. After erosion, surfaces achieve a brilliant finish of the highest quality with only minimal roughness. The effort required for post-processing by grinding or polishing is significantly reduced: precision work, including time savings. EDM machines have long been optimized to be set up with relatively little effort for any desired production part—even small series, prototypes, or individual pieces can now be produced economically.
- Surface roughness up to Ra 0.05 / N2 during erosion
- Achievable tolerances up to +/- 0.001 mm during erosion
- Radii as small as 0.02 mm
- Erosion of small, precise bores
- Erosion of bores as preparation for wire erosion
- Processing of special materials such as ceramics or hard metals
- Processing of other materials: steel, hardened and alloyed or stainless steels (INOX), non-ferrous metals
- Processing in an oil bath: especially for hard metals, ceramics, and corrosion-prone materials
- Manufacturing of micro-clamping tools to fix micro parts for processing
FAQs on Micro Machining
Micro-erosion can process a wide range of conductive materials, including titanium, hardened steel, hard metals, and conductive ceramics. This makes it ideal for demanding applications across various industries.
Micro-erosion at Retero GmbH achieves tolerances of up to +/- 0.001 mm and produces surfaces with minimal roughness. This guarantees the highest precision and quality in the manufacturing of the smallest components.
Thanks to our efficient processes and advanced technologies, we can manufacture your parts quickly and reliably without compromising on quality. The exact production time depends on the specific requirements of your project.
Yes, we offer prototype manufacturing as well as small series production. Our micro-erosion technology is perfect for creating precise prototypes that meet your exact specifications.
Erosion is a simple process: An electrode made of hard metal, silver, or tungsten serves as the tool. It is brought very close to the workpiece without actually touching it. As current begins to flow between the workpiece and the electrode, a spark discharge occurs. This generates extremely high temperatures between 8,000 and 12,000 degrees, causing material to be removed from the workpiece. Any material that conducts electricity can be processed using the erosion method. The amount of material removed depends primarily on the polarity, the gap width between the electrode and the workpiece, as well as the duration and intensity of the process.
These discharges and material removal take place in a special environment, requiring a non-conductive medium such as mineral oil or deionized water. This medium is also known as the dielectric; it is either contained in a basin or delivered to the work area through tubes. The dielectric compensates for the very high temperatures during the erosion process and also transports the removed material away. Therefore, it surrounds both the workpiece and the electrode during the machining process.
Micro-erosion allows for absolutely precise material removal and the execution of complex shapes, delicate contours, tiny radii, and minimal bores. It is suitable for a wide range of industries, including mechanical engineering, medical technology, watchmaking, automotive manufacturing, and aerospace. Additionally, various materials can be eroded, including hard titanium, hardened steel, and ceramics.
Retero offers surface roughness levels up to Ra 0.05 / N2 during erosion and achievable tolerances up to +/- 0.001 mm. Minimum radii are 0.02 mm. The manufacturing technique includes the processing of small, precise bores and preparation for wire erosion. Retero works with a variety of materials such as steel, hardened and alloyed steels (INOX), non-ferrous metals, ceramics, and hard metals. Our company meets the ISO 9001 and ISO 13485 quality standards.
Retero can process parts with wire diameters ranging from 0.02 to 0.10 mm and micro-drillings with carbide electrodes from 0.10 mm and larger. Dimensional deviations are only within a few thousandths of a millimeter, and after erosion, the surfaces are left with a brilliant and high-quality finish.
Micro-erosion enables the machining of very small parts with maximum precision, delicate contours, and tiny bores. Compared to traditional machining techniques like milling or honing, it allows for the creation of complex geometric shapes and extreme precision. Additionally, it permits the processing of a wide range of materials, which is often difficult or impossible with other methods.
Micro-erosion technology is used in various industries, including the electronics industry for the production of tiny components, the medical technology sector for precise implants, the aerospace industry for complex components, and the watchmaking industry for high-quality movements. Additionally, it is employed in the automotive industry, tool and mold making, as well as in the manufacturing of fine mechanical components.
Yes, there are several alternative methods to micro-erosion. These include micro-milling technology, where tiny milling tools are used, micro-drilling with lasers, or micro-cutting with lasers or water jets. Each method has its specific applications and advantages and disadvantages in terms of precision, material processing, and shape complexity. The choice of the right method depends on the requirements of the particular project.
Micro machining refers to the process of creating miniature components with high precision using advanced technologies like CNC machining, micro milling, and micro EDM. It involves removing material at micrometer tolerances to create complex geometries and fine details.
Our micro machining processes work with a wide range of materials, including titanium, stainless steel, aluminum, brass, hardened steel, ceramics, polymers, and composites.
Micro machining is widely used in industries such as medical technology, aerospace, electronics, watchmaking, automotive, and photonics due to its ability to deliver precise and reliable components.
Retero GmbH achieves tolerances as tight as +/- 0.001 mm and surface finishes up to Ra 0.05, ensuring the highest level of precision for even the most complex parts.
Micro machining specializes in creating parts on a much smaller scale, with tighter tolerances and finer surface finishes, whereas traditional machining handles larger components with less stringent precision requirements.
We process parts with wire diameters as small as 0.02 mm and micro drillings starting at 0.10 mm using carbide electrodes.
Yes, we can produce intricate shapes, including delicate contours, minimal radii, and extremely fine bores.
Oil bath processing minimizes heat generation and prevents corrosion, ensuring optimal precision and surface quality for sensitive materials like ceramics and hard metals.
We use cutting-edge CNC micro machining, micro milling, micro EDM, and laser micro machining to deliver unmatched precision and efficiency.
Yes, our micro machining services are ideal for prototyping and small-batch production, offering fast turnaround times and high precision.
Yes, our micro machining services include processing non-metal materials such as polymers and composites, ensuring the same level of precision and quality as with metals.