Wire-cut EDM: basics and application
Wire-cut EDM is a shaping manufacturing process: conductive materials can be cut very precisely on the basis of spark discharge. A sequence of electrical voltage pulses generates sparks transferring material from the workpiece (anode) to a passing wire (cathode) as well as to a separating, non-conductive liquid (dielectric: we usually utilize deionized water or a specific oil). Permanent flushing rinses out the erosion waste from the kerf and cools down the wire.
The EDM process starts at the workpiece: at the edge or at a previously drilled starting hole. The copper or brass wire is adducted very closely – there’s only a narrow gap of about 0.004 mm to 0.5 mm – to the workpiece, so that the electric spark jumps the gap. The material melts and vaporizes. During the cutting process, the EDM wire is pulled through the workpiece by means of two wire guides at a speed of up to 25 m/min. Like this, previously programmed contours or – thanks to tilting the wire – conical shapes can be cut into a workpiece.
How does wire EDM work?
A sequence of electrical voltage pulses generates sparks that transfer material from the workpiece (anode) to a thin passing wire (cathode, will be disposed at the end) and into the dielectric liquid. This is a highly precise process as the spark always jumps the gap at the smallest spot.
What is spark erosion turning and shaping?
EDM machines with a rotary axis also make it possible to produce dynamically balanced parts. Even curved shapes and finish-machined structures can be produced in this way. Thanks to a rotary axis, different angles can be set and surfaces on round parts can be eroded. This makes it possible to produce particularly filigree workpieces and micro parts, as no cutting forces impact on the workpiece. High-tech machines with small wire diameters of 0.03 up to 0.3 mm enable the production of very precision parts with surface qualities below Ra 0.1. The procedure of spark erosion is particularly suitable in combination with carbide – even diamond grinding tools can be profiled and dressed by wire erosion.
By wire-erosion dressing, the most precise true running accuracy of less than 0.002 mm can be achieved, in spite of the highest profile accuracy. Due to the non-contact machining, there is neither thermal influence on the fixation nor particulates in the fixation matrix. This means: no poor grinding results, not even on the first workpieces.
What is EDM?
Spark erosion or electrical discharge machining is used for high-precision material processing. Normally, the electrically conductive workpiece is processed in a non-conductive liquid. We differ in spark erosive cutting (wire erosion) and in spark erosive countersinking (die sinking).
How does spark cutting work?
In electrical discharge machining, the material is removed by brief, local electrical spark discharges. This removal process takes place in an electrically non-conductive aka dielectric fluid (usually deionized water or an extra oil). While die-sinking EDM, both the electrode and the workpiece are arranged in dielectric fluid.
Which materials can be processed by spark erosion?
For die-sinking EDM, electrodes made of graphite, copper, tungsten-copper, or copper-zinc alloys are used. Due to the low wire wear, mainly brass wire – or coated brass wire for high accuracy – is used for wire erosion.
What are the advantages and areas of application of wire erosion?
Spark erosion machining enables the production of minuscule parts with extreme accuracy and high cutting speeds: An electric spark cuts conductive materials such as aluminum, copper, or graphite.
• No material residues and quasi lossless: ideal for expensive materials.
• No contact: very small parts with extremely thin cladding can be cut – without contact between cutting tool and workpiece.
• No fixtures: no special fixtures required – this saves money and increases the flexibility.
• No interruption: these machines run up to 140 hours at a stretch.
• No finishing: flawless surfaces thanks to wire erosion are possible. Surface qualities of less than Ra 0.10 are feasible.
• No tools: only a single, high-quality wire is needed.
How does eroding work?
In this machining process, electrically conductive materials (e. g. aluminum, copper, brass, or steel) are removed by electrical discharge. The advantage: this process is contact-free.
EDM enables highly precise results: very fine and delicate contours, complex geometries, diminutive radii, and bores are as feasible as well as very narrow cutting widths and countersinks. By achieving best surface qualities, the tolerance deviations measure only a few thousandths of a millimeters. Typical ranges of application can be:
• Medical engineering
• Electronics
• Engine & vehicle construction
• Tool & mould design and construction
• Prototyping
• Machine construction
• Aerospace industry
Which materials can be eroded?
Thanks to electric discharge machining, even extremely hard materials such as titanium, hardened steel, special alloys, or conductive high-tensile ceramics can be easily processed and shaped.
What is start-hole EDM?
Start-hole EDM is a fast and particularly economical process for metal machining – very thin or very thick materials can be processed. Thanks to a CNC control with electrode changer, a very fast and precise machining of the materials is practicable. Depending on the range of application and the materials to be processed, appropriate electrodes are utilized. The benefits are obvious: more economical series machining, mitigated error risks, fast workflow, and highly precise results.
Start-hole EDM is a shaping process: conductive materials can be cut very precisely by using the principle of spark discharge. In addition, due to the contact-free machining, there’s no need to worry about mechanical or thermal influences or molecular structural changes of the material.
Thanks to our mold making erosion machines, we are able to guarantee a consistently high precision – even with closest tolerances and tiniest parts. Due to wire erosion, we have the skills to produce very small parts with radii down to 0.009 mm and feasible tolerances down to +/-0.0015mm.
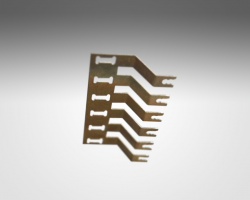
TECHNICAL SPECIFICATIONS FOR WIRE-CUT EDM
- Surface qualities up to Ra 0.1 / N3
- Achievable tolerances up to +/- 0.0015 mm
- Radii up to 0.009 mm
- Tapering +/- 30 degrees until max. 100 mm height
- Wire calibers of 0.15 – 0.30 mm for efficient and precise cutting
- Processing of special materials such as ceramics or hard metals
- Shaping of other materials such as steel or hardened, alloyed, or stainless steels (INOX) and non-ferrous metals
MANUFACTURING MICRO PARTS WITH WIRE-CUT EDM
Thanks to wire-cut EDM, we are able to machine micro parts with radii down to 0.009 mm and achieve narrow tolerances up to +/-0.0015 mm.
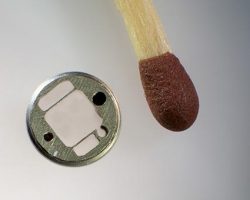