Our new rotary axis allows a wide variety of shapes, very fine recesses, filigree profiles, and small radii or surfaces on round parts – all of them contactless and without force effect on the workpieces. We use the rotary axis if deep, fine recesses or small corner radii on round parts are not feasible anymore.
The rotary axis comes with great benefits, especially in wheel dressing: we are able to insert profiles with finest inner radii of e. g. r = 0.05 mm. Thanks to this process, we guarantee both profile accuracies in the µm range and high concentricity. The only condition is that the workpiece has electroconductive properties. Spark-erosive machining comes with the great advantage that workpiece will not be scalded during the work process. Therefore, there are no structural material changes to worry about.

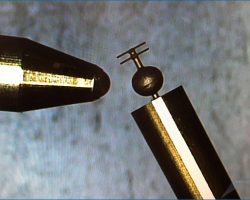
TECHNICAL SPECIFICATIONS FOR ELECTRO-DISCHARGE MACHINING
- High profile accuracy
- High true running accuracy (0.002 mm)
- Realization of most filigree contours
- Deep, fine recesses on round parts with small slot widths
- Finest inner radii for recesses on round parts of r = 0.05 mm
- Surface finishes of Ra 0.1
- Different surfaces and/or widths across can be set and eroded at variable angles
-
- No break out of bond matrix components during the dressing of profile grinding wheels
- Shaping of special materials such as ceramics or hard metals
- Machining/dressing of CBN or diamond grinding wheels (condition: bonding material and carrier are electroconductive)
- Machining of materials such as hardened and alloyed or stainless steels (INOX), non-ferrous metals