CNC Drahterodieren & Drahterosion aus der Schweiz mit Retero – Ihr Hersteller und Dienstleister für Kleinstteile
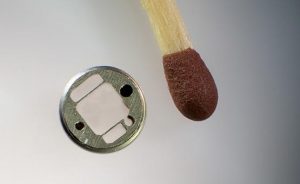
Unsere Mitarbeitenden verfügen über ein aussergewöhnlich grosses Know-how beim Drahterodieren. Dies ist ein formgebendes Fertigungsverfahren: Leitfähige Materialien können hierbei auf dem Prinzip der Funkenentladung sehr präzise geschnitten werden. Zudem gibt es durch die kontaktfreie Bearbeitung weder mechanische oder thermische Beeinflussung noch molekulare Gefügeveränderungen im zu bearbeitenden Material.
Kleinstteile mit Drahterosion herstellen
Dank unseren Formenbau-Erodiermaschinen erreichen wir selbst bei engsten Toleranzen und kleinsten Teilen eine konstant hohe Präzision. Mit Hilfe der Drahterosion können wir Kleinstteile mit Radien bis 0.009mm und erreichbaren Toleranzen von bis +/-0.0015mm hergestellt werden.
Vorteile von Drahterodieren
Eine funkenerosive Bearbeitung ermöglicht die Herstellung sehr filigraner Teile mit grosser Genauigkeit, beachtlicher Schnittgeschwindigkeit und dies über lange Zeit. 140 Stunden Laufzeit sind bei solchen Maschinen kein Problem. Der elektrischer Funke schneidet leitende Materialien wie z. B.
- Aluminium,
- Kupfer oder
- Graphit.
Selbst extrem harte Materialien wie Titan, gehärteter Stahl, Sonderlegierungen oder leitfähige hochfeste Keramiken können problemlos bearbeitet und in die gewünschte Form gebracht werden.
Diese Vorgehensweise ist fast verlustfrei – bei teuren Materialien ein grosser Vorteil. Drahterodieren erfolgt kontaktfrei: Dies ermöglicht das Zuschneiden von sehr kleinen Teilen mit hauchdünnen Wänden. Durch die kontaktfreie Bearbeitung sind zudem weder thermische Beeinflussung der Bindung noch losgebrochene Partikel zu befürchten. Ein weiterer Pluspunkt, denn so lässt sich Geld sparen und flexibler arbeiten. Als «Werkzeug» wird dabei lediglich ein dünner, hochwertiger Draht verwendet. Auch eine zeitintensive Nachbearbeitung entfällt: Drahterosion hinterlässt makellose Oberflächen mit Qualitäten von unter Ra 0.10.
Zusammengefasst
- Keine Materialreste und praktisch verlustfrei: ideal bei teuren Materialien
- Kein Kontakt: Ohne Berührung zwischen Schneidwerkzeug und Werkstück können sehr kleine Teile mit extrem dünnen Wänden geschnitten werden.
- Keine Aufnahmen: Es sind keine speziellen Aufnahmevorrichtungen notwendig – das spart Geld und erhöht die Flexibilität.
- Keine Unterbrechung: Bis zu 140 Stunden Laufzeit am Stück sind kein Problem.
Keine Nachbearbeitung: makellose Oberflächen dank Drahterosion, Oberflächenqualitäten von unter Ra 0.10 - Kein Werkzeug: Zur Drahterosion wird lediglich ein einziger, hochwertiger Draht benötigt.
Anwendungsmöglichkeiten von Drahterodieren
Das Erodieren ermöglicht maximal präzise Resultate: Es können feinste, filigrane Konturen, komplexe Geometrien, kleinste Radien und Bohrungen sowie sehr schmale Schnittbreiten und Senkungen realisiert werden. Bei besten Oberflächengüten betragen die Toleranzabweichungen lediglich wenige tausendstel Millimeter. Erodiermaschinen mit einer Rundachse meistern sogar das Fertigen von rotationssymmetrischen Teilen. So kann man äusserst filigrane Werkstücke und Mikroteile herstellen.
Dieses Verfahren wird eingesetzt in
- der Medizintechnik,
- der Elektronikbranche,
- im Motoren-, Fahrzeugbau,
- der Prototypenfertigung,
- im Maschinenbau sowie
- in der Luft- und Raumfahrt.
Dadurch können genaueste Rundlaufanforderungen von weniger als 0.002 mm erreicht werden – bei maximaler Profiltreue. Moderne Maschinen mit Drahtdurchmessern von 0,03 bis 0,3 mm ermöglichen die Fertigung von Präzisionsteilen mit Oberflächenqualitäten unter Ra 0.1. Besonders geeignet ist die Funkerosion in Verbindung mit Hartmetall – sogar Diamantschleifwerkzeuge können drahterosiv profiliert und abgerichtet werden.
Vorgehen
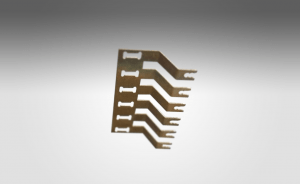
Der Erodiervorgang beginnt am Werkstück, am Rand oder an einer zuvor eingebrachten Startlochbohrung. Der Kupfer- oder Messingdraht wird durch die Maschine bis zu einem schmalen Spalt von 0,004 mm – 0,5 mm an das Werkstück herangeführt, so dass ein Funke überspringt, der das Material aufschmilzt und verdampft. Während des Schneidvorgangs wird derErodierdraht mittels zwei Drahtführungen durch das Werkstück gezogen; diesen Vorgang kontrolliert die Maschine. Während des Bearbeitungsvorganges wird auch der Draht erodiert.
Daher muss von einer Spule kontinuierlich neuer Draht zugeführt werden. Meistens wickelt sich der verschlissene Draht auf eine weitere Spule auf, die hinter der Maschine ist. Der verschlissene Draht wird in den hinteren Bereich der Maschine geführt und mittels eines Messers in kleine Stücke geschnitten oder bei dünnen Drähten direkt in den Abfallbehälter geführt und gesammelt und danach entsorgt. Die Genauigkeit des Verfahrens beruht darauf, dass der Funke stets an derjenigen Stelle überspringt, an der der Abstand zwischen Werkstück und Draht am geringsten ist.
Drahterodieren: Technische Angaben
- Oberflächenrauheiten bis Ra 0.1 / N3
- Erreichbare Toleranzen bis +/- 0.0015 mm
- Radien bis 0.009 mm
- Konizität +/- 30 Grad bis max. 100 mm Höhe
- Drahtdurchmesser von 0.15 – 0.30 mm für effizientes und präzises Schneiden
- Bearbeitung von speziellen Materialien wie z.B. Keramik oder Hartmetallen
- Verarbeitung sonstiger Werkstoffe: gehärtete sowie legierte oder rostfreie Stähle (INOX), NE-Metalle
Häufige Fragen unserer Kunden, die wir gerne beantworten
Ja, das ist möglich – wenn man die entsprechenden Maschinen und Skills dafür hat. Wir haben beides und sind in der Lage, mit Erodierdrähten von nur 0.04 mm im Durchmesser Schlitze bis zu 0.08 mm in Werkstücke zu erodieren. Fragen Sie uns an, gerne erstellen wir Ihnen eine Offerte für Ihr Projekt.
Die Technik in dieser Branche entwickelt sich rasant, immer kleinere Drahtdurchmesser können verarbeitet werden. Dank hochmodernen Hightech-Maschinen und viel Know-how seitens der Retero GmbH sind wir in der Lage, Drähte mit einem minimalen Durchmesser von 0.02 mm einzusetzen und zu verarbeiten.
Auf der Öl-Drahterodiermaschine von Retero GmbH können Oberflächen von Ra 0.08 Güte erreicht werden, mit Wasserbad-Erodiermaschinen sind Ra 0.10 möglich. Diese Werte sind ohne kosten- und zeitintensive Nachbearbeitung erreichbar.
Ja, das ist möglich. Bei Retero GmbH sind wir in der Lage, konische Formen bis zu 30 Grad zu erzielen. Fragen Sie uns an, gerne beraten wir Sie und zeigen wir Ihnen, was alles möglich ist.
Das sagen unsere Kunden über uns:
Sie haben das Problem – RETERO GmbH die Lösung. Wir sind spezialisiert auf die Herstellung von Kleinst- und Mikroteilen aus elektrisch leitenden Materialien, insbesondere aus Keramik und Hartmetallen.
Drahterodieren leicht und verständlich erklärt
Das Drahterodieren ist ein formgebendes Fertigungsverfahren: Leitfähige Materialien können hierbei auf dem Prinzip der Funkenentladung sehr präzise geschnitten werden. Eine Folge von elektrischen Spannungspulsen erzeugt Funken, die Material vom Werkstück (Anode) an einen durchlaufenden Draht (Kathode) und an eine trennende, nicht leitende Flüssigkeit (Dielektrikum: meist deionisiertes Wasser oder ein spezielles Öl) übertragen. Durch permanente Spülung werden der Erodierabfall aus dem Schneidspalt entsorgt und der Draht gekühlt.
Der Erodiervorgang beginnt am Werkstück: am Rand oder an einer Startlochbohrung, die zuvor mit einem Bohrer oder durch Senkerodierung eingebracht wurde. Der Kupfer- oder Messingdraht wird bis zu einem schmalen Spalt von 0,004 mm – 0,5 mm an das Werkstück herangeführt, so dass ein Funke überspringt, der das Material aufschmilzt und verdampft. Während des Schneidvorgangs wird der Erodierdraht mittels zwei Drahtführungen mit einer Geschwindigkeit von bis zu 25 m/min durch das Werkstück gezogen: So können programmierte Konturen in ein Werkstück geschnitten werden. Auch können durch Neigung des Drahtes konische Formen erzielt werden.
Durch eine Folge elektrischer Spannungsimpulse werden Funken erzeugt, die Material vom Werkstück (Anode) auf einen durchlaufenden dünnen Draht (Kathode – wird anschliessend entsorgt) sowie in das Dielektrikum übertragen. Dies ist ein hochpräzises Verfahren: Der Funke springt stets dort über, wo der Abstand zwischen Werkstück und Draht am geringsten ist.
Dank Elektroerosion lassen sich selbst extrem harte Materialien wie Titan, gehärteter Stahl, Sonderlegierungen oder leitfähige hochfeste Keramiken problemlos bearbeiten und in die gewünschte Form bringen. Aluminium, Kupfer, Graphit, Molybdän, Tantal, Wolfram und Iridium sind gängige Drahterosionsmaterialien.
Das Tempo des Vorschubs beim Drahterodieren kann sowohl von der Maschine als auch manuell erfolgen und hängt von der Maximalleistung des Generators der jeweiligen Drahterodiermaschine ab. as Schruppschneiden wird beispielsweise mit 150 mm²/min bis 250 mm²/min und einer durchschnittlichen Bezugshöhe von 60 mm durchgeführt.
Mit dem Drahterodieren können beliebige Profile in Form von Durchgangslöchern eingebracht werden, auch in gehärtete Stahlwerkstoffe oder Hartmetall. Auch die Bearbeitung von schwer zu zerspanenden Werkstoffen ist normalerweise kein Problem. Das Verfahren wird deshalb gerne zur Herstellung von Werkstücken aus Titanlegierungen, Hartstoffen oder auch leitfähigen, hochfesten Keramiken eingesetzt. Selbst die Fertigung äußerst anspruchsvoller, komplizierter Innenformen mit kleinsten Eckenradien und gleichzeitiger hoher Maß- und Formgenauigkeit ist mit dem Drahterodieren realisierbar. Charakteristisch für das Drahterodieren sind nach der Herstellung gleichmäßige Oberflächen mit einer hohen Oberflächenqualität.
Unabhängig von Hersteller und Bauart verwenden Drahterodiermaschinen einen 0,02 bis 0,3 mm dicken Metalldraht als Werkzeug (hier Elektrode). Dieser Draht, der üblicherweise aus Messing besteht, aber auch aus Wolfram oder Stahl gefertigt sein kann, wird von einer Spule abgewickelt und mit Hilfe eines Rollensystems straff gespannt durch das zu bearbeitende Werkstück gezogen. Ober- und unterhalb des Bauteils stützen Drahtführungen den Messingdraht und sorgen für einen geraden Schnitt. Voraussetzung dafür, dass das Drahtschneiden von geschlossenen Öffnungen durchgeführt werden kann, ist eine Startlochbohrung. Hierfür ist es notwendig, vorab eine Bohrung oder ein Senkerodierverfahren durchzuführen.Der Messingdraht wird dann durch das Werkstück in das Loch für den eigentlichen Erodiervorgang eingefädelt. Das Bauteil, das auf einer geeigneten Spannvorrichtung befestigt ist, wird dann in einem Dielektrikum funkenerodiert. Dazu sind die Spannvorrichtungen so einzurichten, dass im kompletten Bearbeitungsbereich eine kollisionsfreie Erosion stattfinden kann.
Durch das Drahterodieren können Oberflächenqualitäten bis Ra 0.1 und Toleranzen von +/- 0.0015 mm erreicht werden. Radien bis zu 0.009 mm und konische Formen bis zu einer Höhe von 100 mm sind ebenfalls möglich. Der Drahtdurchmesser von 0.15 bis 0.30 mm ermöglicht effizientes und präzises Schneiden.
Im medizinischen Bereich wird die Drahterosion häufig für die Herstellung von Endoskopen und anderen medizinischen Kleinstteilen aus leitfähigen Materialien wie Inox eingesetzt. Die präzise Funkenerosion ermöglicht die Fertigung von komplexen Formen und dünnen Wänden, ohne das Material zu beeinträchtigen. Dadurch können hochwertige medizinische Geräte hergestellt werden, die höchste Anforderungen erfüllen.